На страже качества
Главные вкладки
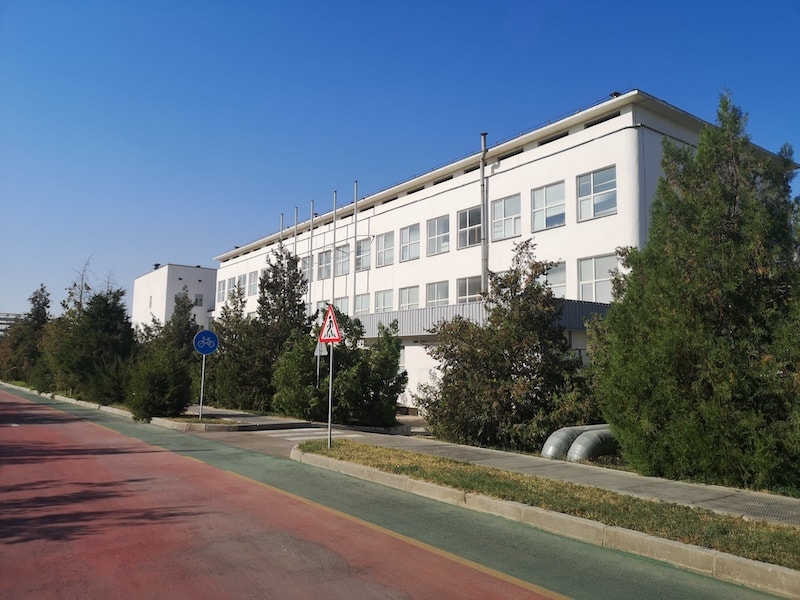
За богатую 35-летнюю историю Шымкентского нефтеперерабатывающего завода не было ситуации, которая бы столь кардинально вторглась в производственную деятельность, как режим ЧП и карантин, объявленные в связи с коронавирусной инфекцией. Но, как отмечают в ШНПЗ, этот сильный внешний фактор не повлиял на главное – штатный режим работы всех структур производства. Нефтяники чтут свою историю, отдают дань своим предшественникам и держат марку важнейшего стратегического объекта Казахстана и поставщика качественных нефтепродуктов для трети потребителей страны.
Более того, в условиях карантина задача бесперебойной работы и сохранения качественных параметров еще более актуализировалась, потребовав от предприятия полной мобилизации. Ключевая же роль в обеспечении качественных показателей отводится заводской лаборатории.
– За всю историю существования завода мы никогда не работали в условиях ЧП, и ни у кого не было подобного опыта. Наша работа в карантин была, действительно, непростой. Мы понимали и возросшие сложности, и возросшую ответственность за качество выпускаемой продукции, – рассказывает менеджер технического контроля Заводской лаборатории ПКОП (ТОО «ПетроКазахстан Ойл Продактс») Ирина Бончук. – Нам не пришлось менять режим, но при этом всю необходимую работу мы выполняли меньшим количеством людей при большей загруженности. При этом часть наших сотрудников работала дистанционно, а часть – находилась в резерве. Нужно отдать должное руководству и администрации завода – они сделали все возможное для бесперебойной работы и выпуска продукции. Мы были обеспечены всем необходимым и в производственном, и в медицинском, и в социальном плане.
Свое летоисчисление ПКОП (ШНПЗ) ведет с 1972 год, когда начались работы по строительству установки ЛК-6У, которую сегодня именуют сердцем завода. Первая нефть была принята заводом в апреле 1983 года. Она поступила из Западной Сибири по трубопроводу «Омск – Павлодар – Чимкент», а спустя несколько дней был отгружен первый состав «черного золота», который ушел на Ферганский НПЗ. С приходом первой нефти строительство комплекса ЛК-6У стало приближаться к завершению. Первый же шымкентский бензин был получен 28 января 1985 года. Эта дата и стала днем рождения Шымкентского НПЗ.
– Заводская лаборатория была сдана в эксплуатацию чуть раньше – в середине 1984 года вместе с рядом основных заводских цехов. Мы вошли в число тех объектов, без которых пуск и дальнейшая эксплуатация установки ЛК-6У и Шымкентского НПЗ в целом были бы просто невозможны, – поясняет Ирина Бончук. – Сегодня заводская лаборатория – это современная, хорошо оснащенная, передовая научно-производственная структура. В нее входят испытательная лаборатория, которой руководит Гульнара Базарбаева, и лаборатория водно-воздушного контроля и реагентов, ее возглавляет
Акмарал Дуйсенбиева. У нас много ветеранов: 17 сотрудников работают со дня основания и успешно передают опыт молодым специалистам. В целом работа коллектива построена на принципах взаимозаменяемости, постоянного обучения и обмена опытом работы.
… Строительство и развитие завода продолжалось еще несколько лет после ввода ЛК-6У: в августе 1985 года были сданы в эксплуатацию еще две секции этой установки. В январе 1986 года запускается газофракционирующая установка. А с весны того же года ШНПЗ начинает работать по полной схеме, доведя мощность переработки до плановых 6 млн тонн в год.
Новый этап истории завода начался с обретением независимости Казахстаном. В феврале 1996 года было образовано АО «Шымкентнефтеоргсинтез» (ШНОС), а в 2005 году компания была приобретена CNPCI – «дочкой» Китайской Национальной Нефтегазовой Корпорации. Два года спустя в состав акционеров вошла НК «КазМунайГаз», получившая 50% доли в пакете. С тех пор основой успеха ПКОП являются два сильных акционера – казахстанская КМГ и китайская CNPC.
Последующие годы ознаменовались масштабными работами по модернизации основных активов предприятия. В 2014 году стартовал Проект реконструкции и модернизации ШНПЗ. Он был нацелен на повышение качества топлива до стандартов К4, К5, экологической безопасности производства и наращивание проектной мощности завода. По своим масштабам Проект сравним со строительством нового НПЗ. Так, за период его реализации было построено 6 новых основных технологических установок, реконструировано порядка 10 вспомогательных блоков и построено свыше 10 объектов общезаводского хозяйства. В 2015 году была введена в эксплуатацию установка производства серы мощностью 4 тыс. тонн в год. А в июне 2017 года на ШНПЗ были введены в эксплуатацию: первая в Казахстане автоматическая установка точечного налива нефтепродуктов, а также установка изомеризации легких бензиновых фракций с блоком предварительной гидроочистки сырья. Фактически был дан старт производства бензинов экологических классов К4 и К5. Таким образом, был успешно завершен первый этап Проекта модернизации ШНПЗ и переход на 100%-е производство высокооктановых автобензинов. В августе 2018 года произошел ряд важных событий в рамках второго этапа Проекта. К началу осени того же года все цели Проекта были достигнуты: объем выработки бензина АИ-92 вырос почти в 3,2 раза по сравнению с домодернизационным периодом, а АИ-95 – в 16 раз!
В настоящее время ПКОП выпускает такие виды нефтепродуктов, как бензины стандарта К4/К5 марок AИ-96, AИ-95, AИ-92, дизельное топливо стандарта К4/К5 марок ДТ-Л, ДТ-Е и ДТ-З; для реактивных двигателей ТС-1, мазут топочный M-100, сжиженный газ и два вида серы.
– Сегодня функции заводской лаборатории расширены: мы должны контролировать качественные показатели всей выпускаемой заводом продукции, как на предмет соответствия техническим условиям, так и требованиям Технических регламентов ЕАЭС. Они едины и обязательны для применения и исполнения на всей территории Союза, – подчеркивает Ирина Бончук. – Контроль непрерывный: НПЗ работает круглосуточно, и нам нужно быть постоянно на страже. И – сквозной: на входе анализируются поступающие на завод нефть и реагенты. Также анализируются все параметры работы технологических установок завода и произведенная товарная продукция. Затем проводится анализ отгружаемой товарной продукции – готовых нефтепродуктов. Контроль качества осуществляется на каждой стадии операции, и именно это позволяет вовремя заметить несоответствия и устранить их, с тем, чтобы на выходе избежать выпуска некачественной продукции. Мы служим качеству – в этом наше предназначение.